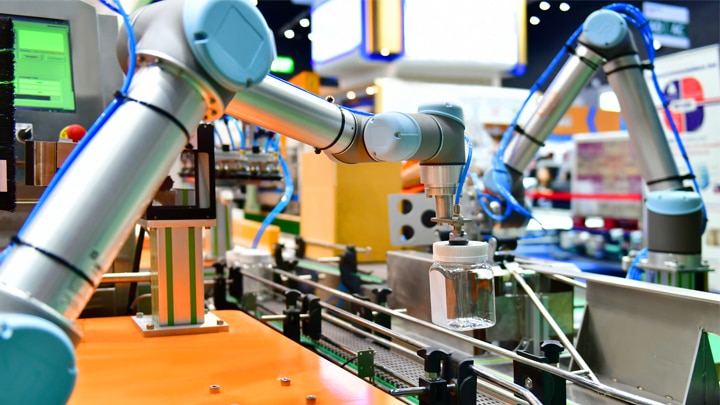
Automation is the way of the future in the manufacturing space. But when it comes to implementation, there is no one-size-fits-all approach. How facilities automate and the speed at which they adopt new technology should be based on each business’ unique goals and the specific needs of its employees. Here are five best practices to guide your automation process, focusing on risk mitigation, worker safety, and business best practices.
5 key practices for manufacturing automation
1. Consider common causes of workplace injury.
One of the primary reasons businesses adopt automation is to reduce workplace injury, which costs manufacturing companies billions of dollars each year.
According to the 2020 Workplace Safety Index, the top causes of workplace injury in manufacturing include: heavy lifting, falls, being hit by an object, being compressed in a machine, or awkward postures that cause deterioration over time, like bending over. In fact, these five causes of injury resulted in more than $5 billion in costs paid out in 2020.
As you adopt new automation technology, consider how automation can support the leading causes of workplace injury in your operation. What technology will best support the health and safety of your specific workforce?
2. Establish your priorities.
As you automate, consider where you need technology most based on the priorities of your business. Automation doesn’t just help improve worker safety – it also can improve production time, reduce waste, help you follow COVID-19 guidelines around social distancing and sanitation, and secure your bottom line. Considering your priorities from both a financial and risk mitigation standpoint can help you determine where and how you should automate in a way that will best support your business goals.
3. Consider lift-assistance equipment.
Heavy lifting is the top cause of workplace injury in factories. Investing in exoskeletons or similar lift-assistance equipment goes a long way toward helping to mitigate risk, reduce costs, and keep workers safe. Adopting lift-assistance technology can also help you optimize your existing labor force, allowing you to move employees away from manual tasks and into other roles you need to fill.
4. Invest in your employees.
Automation allows you to invest in your employees. With machines taking over more repetitive and manual labor, you can train and upskill your employees for more intellectually challenging jobs, like programming. With labor shortages across the manufacturing industry, employees are seeking jobs with growth and training opportunities. When you invest in your employees, you can also improve morale and support your business’ long-term growth.
5. Protect your investment.
Automation is an investment. As you mitigate risk for your workforce, don’t forget to update your insurance coverage to ensure that new technology is protected from loss or damage. And with new manufacturing processes in place, you’ll want to update your coverage around business interruption to help reduce the losses associated with a mechanical breakdown.
An agile approach to automation
There is no single best approach to automation adoption. Taking an agile approach and adopting automation based on business goals and risk assessments will help you automate effectively, while focusing your attention where your business – and your workers – need it the most.
To learn more about why manufacturers are automating, read our article, “How automation in manufacturing can improve worker safety, satisfaction, and productivity.”
Related insights
This website is general in nature, and is provided as a courtesy to you. Information is accurate to the best of Liberty Mutual’s knowledge, but companies and individuals should not rely on it to prevent and mitigate all risks as an explanation of coverage or benefits under an insurance policy. Consult your professional advisor regarding your particular facts and circumstance. By citing external authorities or linking to other websites, Liberty Mutual is not endorsing them.